News
Types of Metal Panel Roll Forming Machine
Types of Metal Panel Roll Forming Machine
The metal panel roll forming machine is an important piece of equipment for any steel-roofing or wall-panel business.metal panel roll forming machine This machinery shapes sheet metal into the desired shape and size while producing more accurate parts than stamping or extrusion. It allows you to work with nearly any type of metal, including ferrous and nonferrous.
There are several different types of roofing and wall panel roll forming machines on the market today. Each has its benefits and disadvantages. If you’re looking to buy a new roll forming machine, it’s important to understand the differences and find the best one for your needs.
Single Profile And Dual Profile Lines
Single profile machines are less expensive than multiple profiles, but they offer the same benefits: ability to process two panel profiles on a single line; less floor space and manpower required; savings in ancillary items; and faster changeovers. However, they typically produce panels at slower speeds than multiple profile lines.
Multi-Panel Roofing and Wall Panel Machines
State-of-the-art multi-panel machines run more sizes, gauges and types of material in up to ten panel configurations. This is ideal for large companies who have a high volume of panel demands and want to save floor space by running more than one coil on the same line.
These systems have a wide range of features, such as automatic sheet loading and punching, double-ended coil rolls, coil cars, turnstiles, a separate drive roller system, and automated changeovers that can occur in 30 minutes. They also can handle a variety of metals and can be used to form both standard and specialty profiles, such as L and J trim.
Shears are incorporated into the front end of most of the roll formers to minimize material waste and increase productivity. This is especially important when a different coil is needed to make a new panel. The shears can be set up to shear in batches of up to five at a time.
Adding in additional automation and technology can also help to improve productivity, cut down on downtime, reduce labor costs, and more. CAD and CAM programs can provide engineers with a virtual version of the production process before the actual machine is installed, making it easier to prevent mistakes or flaws that could lead to costly errors during production.
In addition to saving on costs, these advancements can also help your company’s bottom line by increasing your productivity and lowering your carbon footprint. In fact, these advances can even reduce the environmental impact of your business by cutting down on energy usage and waste.
Portable Rollforming Machines And Prefabricated Panels
If you have a limited budget, purchasing prefabricated panels may be the best option for your business. These products can be made quickly, and you can usually get a deposit back or pay for them through financing.
They’re also easy to transport and store, which can save you a lot of time and money. Additionally, they can help you diversify your business and take on more jobs in different areas of your industry.
Tags:aluminium profile roll forming machine | car panel roll forming machine | container panel machine
0users like this.
- Home
- New products
-
All Products
- Roof sheet roll forming machine
- Double/Three Layer Forming Machine
- Glazed Tile Roll Forming Machine
- C/Z/U Purlin Roll Forming Machine
- Floor Deck/Angle Jch Roll Forming Machine
- Light Steel Keel Roll Forming Machine
- Light Keel Villa House Roll Forming Machine
- Shutter Door and Door Frame Roll Forming Machine
- Roofing Ridge Cap Making Machine
- EPS Sandwich Panel Roll Forming Machine
- Cable Tray Roll Forming Machine
- Highway Guardrail roll forming machine
- Storage Shelves Roll Forming Machine
- Car Carriage Plate Roll Forming Machine
- 3d Wall Panel Roll Forming Machine
- Curving/Arch Roll Forming Machine
- Leveling shearing slitting machine
- Shearing & Bending machine
- Decoiler
- Industry Products
- Video
- Blog
- Contact
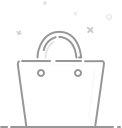
Your cart is currently empty.