News
Sandwich Panel Production Line

Sandwich Panel Production Line
Sandwich panel manufacturing is considered to be one of the most advanced tools in the current market. It is made from high-quality materials and can be installed in a variety of industries. Sandwiches are generally produced for sandwich boards. The high quality and consistency of sandwich boards are what makes it such an important tool in today's industry. When purchasing a sandwich board, always look for high quality equipment for long lasting performance.
Sandwich panels have a dual composite structure that includes layers which are sandwiched together. These sandwich panels are commonly used in the industrial construction industry. Due to the high strength, this type of manufacturing is able to produce high quality boards that are strong enough to withstand many uses and applications. Equipment used in sandwich panel production line is capable of continuous production, so ensuring a steady level of production for many years.
The successive laminating body production line of sandwich panels has different parts, which are used in its manufacturing process. One of the most important parts is the heat laminator. This part works by applying the heat to the sandwich panels during the production process. A heated spot is then applied on top of the hot laminator which causes the top layer to become solid and the bottom layer becomes molten. The molten layer is then pressed against the previously solidified bottom layer and the whole sandwich panel is created.
After manufacturing has been done, the hot lamination system deductions will be released into the cavity. These decoctions will remove any air bubbles that may have remained within the cavities. This will ensure that the smooth surface of the sandwich panels will be unbroken. To add to the quality and consistency of the final product, the heat decoctions must be immediately injected into the cavities and then monitored to ensure that it has been properly contained. If it is not decoiled, then it will cause seepage and air pockets to form between the cooled surface of the decoction and the walls of the cavity. This will then cause bubbles to build up inside the sandwich panels.
There are different processes that are used in sandwich panel production line. Some of the most commonly used processes include gas tumbling, roll forming and mineral wool lamination. For gas tumbling, compressed air is shot into the cavities and the bottom metal will be reshaped into different shapes depending on how the gas goes through the roll forming machine. The roll forming machine will then apply the metal flakes onto the flattened bottom metal and then it will be melted.
For mineral wool lamination, the lower part of the cavity will be wrapped with mineral wool. The upper part will be left free of mineral wool until the formation is complete. Then the upper portion will be coated with a clear resin and then it will be baked at very high temperatures using the roll forming machine. After baking is complete, the upper part will be trimmed to the desired height using the trimming tools and then the cavities will be drilled and filled using the drilling machines. Sandwich panel production line will generally consist of a material feed conveyor and then a material feed cutter to flatten out the material and smoothen the edges before the sandwich forming machine is utilized to apply the desired thickness and surface finish.
Tags:rock wool sandwich panel machine | eps sandwich panel production machine
0users like this.
- Home
- New products
-
All Products
- Roof sheet roll forming machine
- Double/Three Layer Forming Machine
- Glazed Tile Roll Forming Machine
- C/Z/U Purlin Roll Forming Machine
- Floor Deck/Angle Jch Roll Forming Machine
- Light Steel Keel Roll Forming Machine
- Light Keel Villa House Roll Forming Machine
- Shutter Door and Door Frame Roll Forming Machine
- Roofing Ridge Cap Making Machine
- EPS Sandwich Panel Roll Forming Machine
- Cable Tray Roll Forming Machine
- Highway Guardrail roll forming machine
- Storage Shelves Roll Forming Machine
- Car Carriage Plate Roll Forming Machine
- 3d Wall Panel Roll Forming Machine
- Curving/Arch Roll Forming Machine
- Leveling shearing slitting machine
- Shearing & Bending machine
- Decoiler
- Industry Products
- Video
- Blog
- Contact
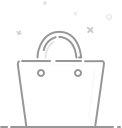
Your cart is currently empty.