News
Corrugated Plate Roll Forming Machine
Corrugated Plate Roll Forming Machine
A corrugated plate roll forming machine can make many types of metal products, from desk drawer slides to construction flashing and even the exteriors of aircraft.corrugated plate roll forming machine This process is known for its high quality, exacting tolerances, rapid production and dimensional accuracy.
There are many different machines available in the market and they all have their own unique characteristics. Before determining which one is the best option for your application, consider the following points:
Power: Does the machine have independent power to all rolls or do you need to purchase a separate motor and drive system? This is important because if the machine doesn’t have enough power to roll your material, it won’t be able to shape it into its desired form.
Capacity: The capacity of a plate rolling machine is determined by the size and pressure (tonnage) it can handle. The larger the machine, the more workpieces it can bend at once. However, the higher the tonnage, the more expensive it is.
Design: A good plate roll will have a few rolls that rotate to shape and crimp the sheet of metal that’s being rolled. The number of rolls depends on the design and how much pressure you need to be able to crimp the metal. The most common are a 3 roll design with a top and pinch roll and a side roller, but some designs have 4-rolls that can be used to form a wide variety of shapes including squares, ovals and hexagonal patterns.
The bending of the metal is controlled by a lower die that opens to a certain width and closes to a certain size. This allows for the smallest of items to be formed, while still maintaining a high level of precision and avoiding any bending problems due to a lack of opening space.
A lubricant is also used in this process to allow the rollers to roll more quickly and easily. The lubricant can be oil, paraffin or other fluids to increase the speed of the machine and help keep the parts in place during bending.
Material: The type of metal you need to roll will determine how much force needs to be applied to the material during the bending process. Some types of metals are more malleable than others at low temperatures and may require more force to form the desired shape.
If you are unsure about the right type of metal to use, talk to your supplier. They will be able to tell you the most efficient and cost-effective way to shape your product.
Pre-feeding: The coils of metal that are fed into the forming machine may need to be punched or notched to remove the coil set before being feed into the forming rollers. The punching process reduces the time needed to prepare the metal for forming and reduces labor costs.
Adjusting the rollers: If you have any issues with the bending of the material, it is a good idea to check the roller adjustments. These can be adjusted to correct for uneven forming areas and gaps between the vertical spaces on symmetrical sections.
Tags:car panel roll forming machine | galvanized steel keel roll forming machine | galvanized panel roll forming machine | rack column roll forming machine
0users like this.
- Home
- New products
-
All Products
- Roof sheet roll forming machine
- Double/Three Layer Forming Machine
- Glazed Tile Roll Forming Machine
- C/Z/U Purlin Roll Forming Machine
- Floor Deck/Angle Jch Roll Forming Machine
- Light Steel Keel Roll Forming Machine
- Light Keel Villa House Roll Forming Machine
- Shutter Door and Door Frame Roll Forming Machine
- Roofing Ridge Cap Making Machine
- EPS Sandwich Panel Roll Forming Machine
- Cable Tray Roll Forming Machine
- Highway Guardrail roll forming machine
- Storage Shelves Roll Forming Machine
- Car Carriage Plate Roll Forming Machine
- 3d Wall Panel Roll Forming Machine
- Curving/Arch Roll Forming Machine
- Leveling shearing slitting machine
- Shearing & Bending machine
- Decoiler
- Industry Products
- Video
- Blog
- Contact
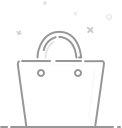
Your cart is currently empty.