News
Choosing a Horizontal Roll Forming Machine
Choosing a Horizontal Roll Forming Machine
A horizontal roll forming machine can be an efficient way to form large sheets of metal. With a self-feeding machine, it can reduce labor costs while reducing scrap. This process also requires fewer moving parts, which reduces the cost of component replacement and tool wear. It can also produce parts with superior jointing qualities. If you're planning to purchase a horizontal roll forming machine, here are some tips that will help you make the best choice:
To make long horizontal sheets of metal, a roll forming company feeds it into a roller system. The first set of rollers grips the strip horizontally in the middle, while subsequent rollers change positions and form a backward C. After that, the strip is cut to the length needed. Then, the finished product is ready for inspection and production. However, metal thickness greater than.0753 inch can cause cracking and may not be suitable for all applications.
It's also critical to understand the nuances of vertical centers and vertical distance. The vertical center distance refers to the distance between the top and bottom shaft centerlines. Once the upper and lower shafts are fully adjusted, the roll former reaches its full vertical range. Another important consideration when choosing a horizontal roll forming machine is tooling quality. The material quality should be a factor, as well. However, if your material quality is poor, you'll need to adjust the tooling.
Make sure you measure the thickness of the material to be roll formed. If you're buying an older roll former, the gap between the top and bottom rolls may be too wide. You need to measure the material's thickness, and this should be documented in a setup sheet. After the material is formed, the machine will need maintenance. If it's not maintained properly, it may not produce the best results. If you need your metal to be as thin as possible, choose a thinner material or an oversized one.
Having a trained operator is essential for a successful roll forming operation. Operators must be capable of handling the machinery, feeding materials into the machine, and adjusting roll centers. During operations, the operator must also understand machine safety and maintain proper maintenance. Proper training is essential for operators and technicians alike. If you're having difficulty setting up the machine, don't hesitate to seek the assistance of a skilled technician.
The process of roll forming begins with a large sheet of metal. Coils can range from one inch to thirty inches wide and 0.012 inch to 0.2 inch thick. The coils must be cleaned and prepared. Each step of the process is represented in a diagram. Eventually, the sheet metal will be discharged. If you're looking for a unique metal profile, roll forming can be the way to go.
Model DH Roll Forming Machine is a versatile tool that's used for manufacturing panel type profiles. Its dual roll forming heads allow you to rapidly adjust the width of the panels. These versatile machines can produce up to eight pieces per minute. The model is especially designed for door panels, appliances housings, and office equipment components. A horizontal roll forming machine with a two-head design allows for easy adjustability of the width.
0users like this.
- Home
- New products
-
All Products
- Roof sheet roll forming machine
- Double/Three Layer Forming Machine
- Glazed Tile Roll Forming Machine
- C/Z/U Purlin Roll Forming Machine
- Floor Deck/Angle Jch Roll Forming Machine
- Light Steel Keel Roll Forming Machine
- Light Keel Villa House Roll Forming Machine
- Shutter Door and Door Frame Roll Forming Machine
- Roofing Ridge Cap Making Machine
- EPS Sandwich Panel Roll Forming Machine
- Cable Tray Roll Forming Machine
- Highway Guardrail roll forming machine
- Storage Shelves Roll Forming Machine
- Car Carriage Plate Roll Forming Machine
- 3d Wall Panel Roll Forming Machine
- Curving/Arch Roll Forming Machine
- Leveling shearing slitting machine
- Shearing & Bending machine
- Decoiler
- Industry Products
- Video
- Blog
- Contact
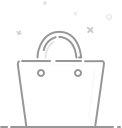
Your cart is currently empty.