News
Using a Metal Sheet Profile Roll Forming Machine
Using a Metal Sheet Profile Roll Forming Machine
Using a metal sheet profile roll forming machine can help produce a smooth and precise contour. This type of forming produces less scrap than other metal working processes. The process is also energy efficient. It requires less heat than other methods and creates clean contours.
Roll forming can be used to form a wide variety of profiles. One common profile is the box profile. It has a capillary groove along the bottom edge that allows the strip to be sealed without the need for additional sealing. Another option is a ribbed profile. Alternatively, a machine can be equipped with side rolls to provide greater precision.
The size and complexity of the cross-section of a component will affect its compatibility with a roll forming line. The yield strength of the material will also affect the number of bends required to shape it. Materials with higher yield strengths require more work to form than materials with lower yield strengths. The number of forming stations increases with the height of the profile. A complex profile with 12 or more bends may require 20 tooling passes.
In addition to producing a variety of cross-sections, the machine can punch holes in the metal and enclose shapes. In some cases, the metal can be coated with paint or varnish. Some machines are available with hydraulic shears to cut metal before going through the forming stations. The pre-cut shear offers a cleaner cut to a flat metal surface. The length of the cut can be determined through a touch screen on the control box.
Aside from the complexity of the profile, another factor is the thickness of the metal. For example, aluminum alloy sheet parts are generally no thicker than 0.125 inches, but they can be as wide as 20 inches. The yield strength of the metal will also affect the production rate of the roll forming line. Stainless steel requires twice as much force as mild steel. Depending on the type of steel used, the production rate of a roll forming line can range from 5 feet per minute to 500 feet per minute.
Other applications that can be performed on a roll forming line include: slitting, punching, and cut to length. Some lines even incorporate all of these applications into a single line. These systems can be configured with a "flying cut off" to allow for cutting while the sheet metal is moving through the roller dies. These systems increase throughput and reduce the need for secondary processing.
Most sheet metal forming machines are designed for a certain range of thicknesses. A roll forming machine can handle coils that are as thin as 0.012 inches and as thick as 30 inches. The thickness of the metal will vary, though. For example, an aluminum alloy sheet part's width will typically be around 0.004 inches to 0.1 inches. The thickness of a mild steel sheet will depend on its yield strength.
There are several different types of metal sheet profile roll forming machines. Most are simple start-up machines that are designed for the small business, while some can be used in full-scale manufacturing facilities.
Tags:upright post roll forming machine | horizontal roll forming machine | step ladder roll forming machine
0users like this.
- Home
- New products
-
All Products
- Roof sheet roll forming machine
- Double/Three Layer Forming Machine
- Glazed Tile Roll Forming Machine
- C/Z/U Purlin Roll Forming Machine
- Floor Deck/Angle Jch Roll Forming Machine
- Light Steel Keel Roll Forming Machine
- Light Keel Villa House Roll Forming Machine
- Shutter Door and Door Frame Roll Forming Machine
- Roofing Ridge Cap Making Machine
- EPS Sandwich Panel Roll Forming Machine
- Cable Tray Roll Forming Machine
- Highway Guardrail roll forming machine
- Storage Shelves Roll Forming Machine
- Car Carriage Plate Roll Forming Machine
- 3d Wall Panel Roll Forming Machine
- Curving/Arch Roll Forming Machine
- Leveling shearing slitting machine
- Shearing & Bending machine
- Decoiler
- Industry Products
- Video
- Blog
- Contact
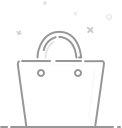
Your cart is currently empty.