News
The Basics of a Roll Forming Machine
The Basics of a Roll Forming Machine
Roll forming machines are designed to bend metal strips into a specific shape or design.trapezoid roll forming machine The process is simple, but it has many different components that work together to ensure the end result is correct and meets a wide range of specifications.
A roll forming machine bends metal at room temperature using several stations where fixed rollers guide the strip and make the necessary bends to form a part.trapezoid roll forming machine This progressive method of bending keeps the cross-sectional area of the part consistent, while maintaining accuracy.
The number of bending stations in a machine depends on the desired size and shape of the final product.trapezoid roll forming machine This means that a machine with more bending stations can produce more complex shapes and patterns than one with fewer stations.
Some materials are more malleable or softer than others and may require fewer bending stations.trapezoid roll forming machine Other machined materials such as black steel, galvanized steel, color coated steel, stainless steel, aluminum and copper respond differently to the rolling forming stress and may need more bending stations or a higher speed to produce an accurate part.
Once the metal is bent, it passes through a series of straightening dies and side rollers to eliminate any lingering twist, bow or camber that could compromise the end result. These distortions can ruin a perfectly good part, so the straightening process is vital to achieving a smooth finish on any metal product.
Another important step in the rolling forming process is the cutting of the finished product. The machine can cut the shaped piece into any desired length with precision and ease. This process is often performed in a flying cutoff press.
Depending on the material and the required shape and length of the metal, some forming machines are designed with specific features that enhance efficiency and accuracy. These include programmable logic controllers that tighten tolerance levels to minimize errors, and laser or TIG welding capabilities. These options can save time by eliminating the need to re-form the part once it's cut.
In addition to these standard features, some forming machines offer additional options that enhance the production process. These include a hydraulic cutter, which is useful for producing smaller pieces of metal such as flashings or small parts that need to be cut from a single sheet. This option allows the manufacturer to make more efficient use of their equipment and increase production efficiency while maintaining accuracy.
There are also a variety of forming machines that allow the user to change the profile of the metal they are making. This is helpful for creating a wide variety of products and is especially useful for building metal roofing sheets in different profiles.
For example, a machine can make ribbed roofing sheets that can be used for standing seam metal roofs. These can be more durable than traditional shingles and can also add value to the property they are used on.
Trapezoid roofing sheets are popular for both commercial and residential buildings. These panels can be made of a variety of types of metal and are easy to install. They are also available in a variety of colors and designs. This type of metal roof is highly durable and is a great option for any building project.
Tags:cz channel roll forming machine | horizontal roll forming machine
0users like this.
- Home
- New products
-
All Products
- Roof sheet roll forming machine
- Double/Three Layer Forming Machine
- Glazed Tile Roll Forming Machine
- C/Z/U Purlin Roll Forming Machine
- Floor Deck/Angle Jch Roll Forming Machine
- Light Steel Keel Roll Forming Machine
- Light Keel Villa House Roll Forming Machine
- Shutter Door and Door Frame Roll Forming Machine
- Roofing Ridge Cap Making Machine
- EPS Sandwich Panel Roll Forming Machine
- Cable Tray Roll Forming Machine
- Highway Guardrail roll forming machine
- Storage Shelves Roll Forming Machine
- Car Carriage Plate Roll Forming Machine
- 3d Wall Panel Roll Forming Machine
- Curving/Arch Roll Forming Machine
- Leveling shearing slitting machine
- Shearing & Bending machine
- Decoiler
- Industry Products
- Video
- Blog
- Contact
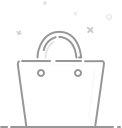
Your cart is currently empty.