News
The Basics of a Metal Sheet Profile Roll Forming Machine
The Basics of a Metal Sheet Profile Roll Forming Machine
The basic concept of a metal sheet profile roll forming machine is to bend and shape metal into a desired shape.metal sheet profile roll forming machine Its design is based on a variety of factors, including the size and complexity of the component and the strength of the metal.
This process can be used to form a wide variety of metal products, from garage doors to metal roofing panels. One of the best things about this particular process is that it does not require much finishing work. Compared to other processes, roll forming requires less energy and produces lower amounts of scrap.
Roll forming uses a combination of several elements, including a large coil of sheet metal and a set of rollers. While there are other ways to shape metal, roll forming produces clean contours and high strength.
A roll forming machine has four main parts: the main base, the entry section, the main rollers, and the auxiliary rolls. Each has a separate function. Some of the machines have a hydraulic tank, which makes the process faster. Others feature laser welding and TIG welding capabilities. These processes remove the need for conventional stamping, reducing labor costs and energy consumption.
The number of forming stations increases with the height of the profile. Profiles with a higher number of bends require more forming stations. However, there are many variables that are considered when calculating the number of forming stations required. In addition, the thickness of the metal and its yield strength can affect the amount of work needed to create the desired shape.
The number of rollers also depends on the complexity of the steel profile. For instance, a narrow profile requires few tooling passes, while a complex one may need up to twenty. There are also other aspects to consider, such as the angle of bending and the distance between the rollers.
There are also programmable logic controllers to help keep the accuracy of the process at an appropriate level. This ensures that the best possible shape is produced, while also avoiding any breaks in the process. Another aspect is the amount of lubrication. Lubrication helps reduce friction between the rolls and the material. If this is not done, it can lead to more wear and tear for the rollers.
Other components that are often seen in roll forming are a cool water level, a safety guard for the body of the machine, and a pre-cut shear. These devices make it easy to cut the metal to the desired length while it is moving through the forming dies.
The computer can determine the optimal position of the rollers to produce the best shape. In addition, CAD renderings can show any flaws that are present before the actual production. Lastly, the Flying Cut-Off allows the cutting of the shape to be performed while the incoming metal is still shaped by the rollers.
Roll forming is a fast and effective method of forming a variety of shapes and sizes. However, it is important to keep in mind that the process is not a simple task.
Tags:galvanized sheet making machine | upright post roll forming machine
0users like this.
- Home
- New products
-
All Products
- Roof sheet roll forming machine
- Double/Three Layer Forming Machine
- Glazed Tile Roll Forming Machine
- C/Z/U Purlin Roll Forming Machine
- Floor Deck/Angle Jch Roll Forming Machine
- Light Steel Keel Roll Forming Machine
- Light Keel Villa House Roll Forming Machine
- Shutter Door and Door Frame Roll Forming Machine
- Roofing Ridge Cap Making Machine
- EPS Sandwich Panel Roll Forming Machine
- Cable Tray Roll Forming Machine
- Highway Guardrail roll forming machine
- Storage Shelves Roll Forming Machine
- Car Carriage Plate Roll Forming Machine
- 3d Wall Panel Roll Forming Machine
- Curving/Arch Roll Forming Machine
- Leveling shearing slitting machine
- Shearing & Bending machine
- Decoiler
- Industry Products
- Video
- Blog
- Contact
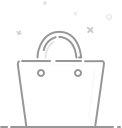
Your cart is currently empty.