News
Selecting a Metal Profile Roll Forming Machine
Selecting a Metal Profile Roll Forming Machine
Using a metal profile roll forming machine, sheet metal can be formed into complex shapes without cracking or breaking. The process uses successive sets of mated rolls, each making small changes in the shape of the profile. When combined, these slight adjustments create the complete profile. The metal is then cut to length and discharged from the line. This manufacturing process has many benefits and is often used for production of profiles such as drywall corners, metal ceilings, metal door frames, metal furniture and racking systems.
In addition to creating precise parts with a high degree of accuracy, metal profile forming machines offer significant productivity. This is due to the fact that these types of equipment can perform multiple applications in one line. Examples of this include punching, notching and cutting. This makes it ideal for producing high volume profiles like stair rails, ductwork, metal curtain walls and racking systems.
Some of the most important features to consider when selecting a metal profile roll forming machine are its automation capabilities, material handling, and integrated cutting or punching units. These functions can help reduce downtime, improve safety, and streamline the overall production process. A machine with these features may be more expensive than a standard model, but the investment can be well worth it in terms of increased efficiency and precision.
Other factors to consider include the type of work material and its reaction to the stresses imposed by the forming process. Some materials are more malleable, or softer, than others. This can affect the number of bending stations required, as well as the overall profile. Black steel, galvanized steel, prepainted steel, stainless steel, aluminum and copper all react differently when subjected to the bending stresses of roll forming. This is why it is important to work with an experienced metal forming OEM that understands these differences and can provide the best possible tooling designs for each type of work material.
The type of cooling system can also have a major impact on the profile quality and longevity. Flood cooling extends tooling life, but it can lead to a buildup of heat and distortion in the profile. In contrast, dry cooling provides a cleaner surface for the finished product but can shorten tooling life. Lastly, the design of the roll tooling itself is a crucial factor in the final profile quality and cost. Different types of work metal require different types of roll tooling steel and undergo different postprocesses, including hardening and chrome plating. An experienced metal forming OEM can help with this selection and design to achieve the desired profile quality at a minimum cost.
Another way to lower the initial investment is to choose a rafted system, where the entire tooling is loaded onto the shafts and preset. This eliminates the need for an operator to manually change the roll tooling from one profile to another, reducing mistakes that can be made during the process. This is an especially important consideration for fabricators that manufacture a variety of profiles.
Tags:car body panel roll forming machine | container board roll forming machine | ceiling stud and track roll forming machine | profile steel making machine
0users like this.
- Home
- New products
-
All Products
- Roof sheet roll forming machine
- Double/Three Layer Forming Machine
- Glazed Tile Roll Forming Machine
- C/Z/U Purlin Roll Forming Machine
- Floor Deck/Angle Jch Roll Forming Machine
- Light Steel Keel Roll Forming Machine
- Light Keel Villa House Roll Forming Machine
- Shutter Door and Door Frame Roll Forming Machine
- Roofing Ridge Cap Making Machine
- EPS Sandwich Panel Roll Forming Machine
- Cable Tray Roll Forming Machine
- Highway Guardrail roll forming machine
- Storage Shelves Roll Forming Machine
- Car Carriage Plate Roll Forming Machine
- 3d Wall Panel Roll Forming Machine
- Curving/Arch Roll Forming Machine
- Leveling shearing slitting machine
- Shearing & Bending machine
- Decoiler
- Industry Products
- Video
- Blog
- Contact
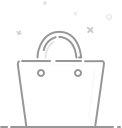
Your cart is currently empty.