News
Rack Roll Forming Machine
Rack Roll Forming Machine
A rack roll forming machine, also known as an upright rack roll forming machine or rack column forming machine, produces industrial-grade storage racks for warehouse and factory applications.rack roll forming machine They vary in size and design to meet a wide variety of loading capacities and styles. They can be produced in a single production line with punching holes and slots, or they can be custom-designed to produce specific sizes and shapes.
The basic roll forming machine consists of an entry section, station rollers and a mill section where the metal is progressively shaped. A typical roll form line may consist of one or more punch presses in the entry section and a series of 10-24 pairs of roller die stands in the mill.
Using computer-aided tooling designs, these machines function at their highest potential and minimize errors, reducing cost. They can eliminate secondary fabrication steps by design, such as laser welding or TIG welding, and rely on computer-controlled programming to tighten tolerance levels.
Some roll forming machines have a strip accumulator or slack loop stand that allows the coil strips to stop for pre-punch press strokes without wasting valuable time in between operations. This feature contributes to the high-speed efficiency of roll forming, since it can temporarily store sections of metal strip so that the mill can continue working while the loop straightens out.
Another advantage of a strip accumulator is that it can be used for both high- and low-speed operations. This is important for a metal forming machine that runs at high speeds, because frequent stopping and starting can cause the coil to break and the operation to stop running.
Today's strip accumulators use high-speed, programmable control to automatically feed a segment of slack at the right time to help keep the operation running efficiently. Some strip accumulators are even equipped with automatic cut off presses that can cut the part to length without disrupting the roll forming process.
When designing a roll forming machine, you should consider the following components:
Uncoiling, leveling and punching Holes and Slots.
Depending on the type of machine and customer's specifications, the uncoiling step can be automated or manual. The punching hole press can be servo-driven or manually fed.
The servo feeder can be operated in a single or multistage, so that different widths of the metal can be fed at the same time into the punching die.
It is equipped with a high-strength steel channel structure, which has a high strength and long service life. The punching die is made of GCr15, quenching and hardening, abrasion-resistant steel, which has a good anti-rust performance.
After roll forming, the part is run through a series of straightening dies and side rollers to remove any lingering twist, bow or camber that can ruin a perfectly good product. This is a critical step, as these imperfections can make a shaped piece look unsightly and reduce its functionality.
In addition to the aforementioned components, most roll forming machines are designed with a flying cut off press that cuts the metal to length without interrupting the forming process. Whether the resulting length cut is short or long, this step ensures that the part is perfectly uniform throughout.
0users like this.
- Home
- New products
-
All Products
- Roof sheet roll forming machine
- Double/Three Layer Forming Machine
- Glazed Tile Roll Forming Machine
- C/Z/U Purlin Roll Forming Machine
- Floor Deck/Angle Jch Roll Forming Machine
- Light Steel Keel Roll Forming Machine
- Light Keel Villa House Roll Forming Machine
- Shutter Door and Door Frame Roll Forming Machine
- Roofing Ridge Cap Making Machine
- EPS Sandwich Panel Roll Forming Machine
- Cable Tray Roll Forming Machine
- Highway Guardrail roll forming machine
- Storage Shelves Roll Forming Machine
- Car Carriage Plate Roll Forming Machine
- 3d Wall Panel Roll Forming Machine
- Curving/Arch Roll Forming Machine
- Leveling shearing slitting machine
- Shearing & Bending machine
- Decoiler
- Industry Products
- Video
- Blog
- Contact
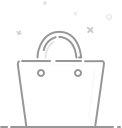
Your cart is currently empty.