News
How to Design a Curving Roll Forming Machine
How to Design a Curving Roll Forming Machine
When determining the right curving roll forming machine, consider the types of materials that are frequently curved. A high-strength steel, for example, requires greater overbend and higher springback than other materials. In addition, it lacks support in the leading and trailing edges, which makes it more difficult to control quality. A rafted system also reduces errors during manual tooling changes, including incorrect gap settings.
Production rates are based on the material thickness, bend radius, and number of stations required. For example, a low carbon steel with 50 times bend radius can be processed at speeds of 85 feet per minute through eight stations. For a 22-station machine, the rate may increase to 55 feet per minute. The production rate can be increased for punching applications as well. However, in some cases, a high speed line can limit the speed of a curved roll forming machine.
After establishing the material and process parameters, the industrial designer can proceed to the design stage. The first step in designing a curve is to create a rough idea of the part. A rough sketch of the material and the thickness will give the designer a general idea of the concept's limitations. Closed profiles and deep, narrow folds are discouraged and symmetry is preferred whenever possible. In many cases, a cross-sectional arrangement of a part can serve as a starting point for a curving roll forming machine.
Once the design phase is complete, the process is timed to prevent tool wear and tear. The tools are designed to last for several hundred thousand cycles, but lubrication is essential to minimize tool wear and maximize the speed of the process. Some models are also equipped with hydraulic tanks to automate the shears. In addition, hydraulics can make the machine faster and easier to maintain. This process is a complex process that requires a highly skilled operator.
The process begins with a large sheet metal coil. These coils can be from one inch to 30 inches wide and 0.012 inch to 0.2 inch thick. The coils must be properly prepared for the process. The diagram above shows each step in the process. At the end, the material is cutoff and discharged. While this might seem like an insignificant detail, it is important to remember that the forming process can handle virtually any material. Ferrous and non-ferrous metals are both suitable for the process.
Roll forming machines are versatile, allowing manufacturers to produce shapes with different thicknesses and materials. The tooling used to make these profiles involves carefully crafting the roll tools. The process begins with a flower pattern, which consists of multiple cross-sections one for each stand of rolls. From the flower pattern, roll contours are derived. Often, computer simulation is used to design roll tools and optimize the forming process.
Another type of curving roll forming machine is a punching machine. The tooling on a punching machine helps a sheet metal achieve its desired shape. As the metal rolls under the steel rolls, the tooling is changed. The first roll cuts four-line indentations, while the subsequent rolls make six-line impressions and begin curving the raised sections. Before making a decision about which type of curving roll forming machine to choose, consider the benefits and drawbacks of each approach. The former option eliminates the need for expensive cutoff dies. In addition, the latter method also requires a precut shear, which allows hand-feeding strips or sheets.
Tags:l angle roll forming machine | ibr roll forming machine | ibr sheet roll forming machine | rack column roll forming machine
0users like this.
- Home
- New products
-
All Products
- Roof sheet roll forming machine
- Double/Three Layer Forming Machine
- Glazed Tile Roll Forming Machine
- C/Z/U Purlin Roll Forming Machine
- Floor Deck/Angle Jch Roll Forming Machine
- Light Steel Keel Roll Forming Machine
- Light Keel Villa House Roll Forming Machine
- Shutter Door and Door Frame Roll Forming Machine
- Roofing Ridge Cap Making Machine
- EPS Sandwich Panel Roll Forming Machine
- Cable Tray Roll Forming Machine
- Highway Guardrail roll forming machine
- Storage Shelves Roll Forming Machine
- Car Carriage Plate Roll Forming Machine
- 3d Wall Panel Roll Forming Machine
- Curving/Arch Roll Forming Machine
- Leveling shearing slitting machine
- Shearing & Bending machine
- Decoiler
- Industry Products
- Video
- Blog
- Contact
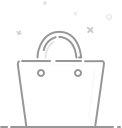
Your cart is currently empty.