News
How a Metal Profile Roll Forming Machine Works
How a Metal Profile Roll Forming Machine Works
The metal profile roll forming machine is used to produce different types of metal shapes. These shapes are made from long coils of raw steel that are fed into the machine. The forming process takes place in a controlled environment to ensure that the parts are made with the proper geometry and thickness for their intended use. The resulting metal products are lighter, stronger, and more cost-effective than cast parts. These benefits make the process well suited for high-volume production applications. In addition, the manufacturing process uses a minimal amount of energy and eliminates the need for cooling or heating of the material.
Unlike casting, which is better suited for low-volume batch production, the forming process is very efficient for high-volume orders of 10,000+ parts. This makes it a great option for companies producing a variety of different types of metal channels, which may require complex bends, holes, notches, knockouts, stamping, or embossing.
The forming process is highly repeatable, which helps to reduce the number of mistakes in the final product. This is particularly important when producing large quantities of the same part. In order to achieve this, the machine must be set up with a precise geometry and an accurate die setup. The machine must also have a control system that can handle the high volume of work.
A PLC is a specialized computer control that can monitor the forming process and make adjustments as needed. These systems can also help to automate certain functions that are traditionally performed by hand. These include punching and cutting the metal sections to a specific length.
During the pre-feed process, a strip of steel is prepared for the forming process. Coils of metal often become "set" in storage and must be unwound prior to machining. The coils are then fed into a pre-feed roller that removes the set and flattens the lead end. It may also be tapered for smooth feeding into the forming station. Applications such as punching or notching can also be added to the pre-feed process.
Once the finished part is formed, it is cut off of the line using a flying cutter. This style of cutting allows for cutting while the system is still moving the metal through the roller dies, which increases throughput and minimizes the amount of manual supervision required.
If you are in the market for a metal profile roll forming machine, look for one that is well-maintained and has a good track record of reliability. Check for signs of wear and tear, such as rusting. This is a sign that the machine has been in service for some time and may have been exposed to harsh environmental conditions. A well-maintained machine should last for years, but it's a good idea to take the time to look it over carefully before making any decisions. It's possible that a slightly older machine could be just as reliable and affordable, but it's a good idea not to settle for anything less than the best.
Tags:shelf column roll forming machine | aluminium profile roll forming machine | cable bridge roll forming machine | storage shelves roll forming machine
0users like this.
- Home
- New products
-
All Products
- Roof sheet roll forming machine
- Double/Three Layer Forming Machine
- Glazed Tile Roll Forming Machine
- C/Z/U Purlin Roll Forming Machine
- Floor Deck/Angle Jch Roll Forming Machine
- Light Steel Keel Roll Forming Machine
- Light Keel Villa House Roll Forming Machine
- Shutter Door and Door Frame Roll Forming Machine
- Roofing Ridge Cap Making Machine
- EPS Sandwich Panel Roll Forming Machine
- Cable Tray Roll Forming Machine
- Highway Guardrail roll forming machine
- Storage Shelves Roll Forming Machine
- Car Carriage Plate Roll Forming Machine
- 3d Wall Panel Roll Forming Machine
- Curving/Arch Roll Forming Machine
- Leveling shearing slitting machine
- Shearing & Bending machine
- Decoiler
- Industry Products
- Video
- Blog
- Contact
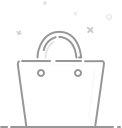
Your cart is currently empty.