News
How Does an Aluminum Roll Forming Machine Work?
How Does an Aluminum Roll Forming Machine Work?
Roll forming is a continuous bending operation ideal for making components that have a consistent profile running the entire length of the part.aluminum roll forming machine This method is much faster than the press brake method and produces far fewer waste materials. The tight cross sections produced by roll forming also require very little, if any, finishing work.
The process works by a coiled sheet metal being fed through a series of roller dies that gradually bend the sheet metal into a profile.aluminum roll forming machine The resulting profile can be a straight or a curved one and may have an open or closed section. The profiles created can be used for a wide range of applications including commercial building, automotive, and industrial use.
Almost any material that can be bent to a specified radius can be roll formed, including both ferrous and nonferrous metals.aluminum roll forming machine The material can be a hot or cold rolled piece of sheet metal that is either unpainted, plated, or coated. The resulting products are very strong and attractive with very tight tolerances and clean contours. The shaped product is less expensive than other types of fabricated metals and requires minimal finishing.
In the case of aluminum, it has a low weight, excellent corrosion resistance and an attractive appearance that can be highly finished with painting or other coatings. Compared to a comparable steel product, aluminum can save between 30% and 40% in manufacturing costs due to its lower weight.
Most of the materials that are roll formed can be connected to other parts using a variety of methods, such as welding (for example MIG), plug-in/screw connections, junction element connections, rivet connections or press connection. In addition, the end-products usually only need to be cleaned or lubricated to prepare them for shipment. This makes the product a cost-effective choice for many different industries.
Adding in-line operations, such as punching or notching, can speed up the processing time. This helps to reduce the amount of labor required and eliminates the need for secondary processes. Flying cut-offs can also be added to the machine which cuts the shapes at precise lengths while they are still moving through the roller dies, significantly increasing production rates.
The beginning of a coil of metal often needs to be conditioned in order for it to easily feed into the machine. This is done by a pre-press process, which can include tapering the lead end, removing any coil set and reducing the tension of the material. A decoiler or upender can also be installed to remove a partially used coil and allow new coils to be loaded while the line is still running, saving 10-15 minutes per coil change.
Once the metal is finished with its run through the roller dies, it can be cut to a specific length by a cutting station. The system can also be equipped with a conveyor which allows the finished pieces to be automatically transferred to a storage rack or other handling device for further processing.
0users like this.
- Home
- New products
-
All Products
- Roof sheet roll forming machine
- Double/Three Layer Forming Machine
- Glazed Tile Roll Forming Machine
- C/Z/U Purlin Roll Forming Machine
- Floor Deck/Angle Jch Roll Forming Machine
- Light Steel Keel Roll Forming Machine
- Light Keel Villa House Roll Forming Machine
- Shutter Door and Door Frame Roll Forming Machine
- Roofing Ridge Cap Making Machine
- EPS Sandwich Panel Roll Forming Machine
- Cable Tray Roll Forming Machine
- Highway Guardrail roll forming machine
- Storage Shelves Roll Forming Machine
- Car Carriage Plate Roll Forming Machine
- 3d Wall Panel Roll Forming Machine
- Curving/Arch Roll Forming Machine
- Leveling shearing slitting machine
- Shearing & Bending machine
- Decoiler
- Industry Products
- Video
- Blog
- Contact
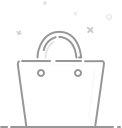
Your cart is currently empty.