News
Curving Roll Forming Machine
Curving Roll Forming Machine
If you need to manufacture a part with a curved profile, you can use a curving roll forming machine. This machine makes bends by rolling a sheet of metal at a specific speed. Its production rate depends on the material thickness, number of stations, and bend radius. For example, low carbon steel with a bend radius of 50 times can be produced at up to 85 feet per minute through eight stations and 55 feet per minute through twelve stations. Its production rate can be anywhere from five to five hundred feet per minute depending on the number of stations used. The production rate of a curving roll forming machine depends on the particular application.
A curving roll forming machine consists of a series of roller die stands that are individually or gang driven. The rolls are designed by following a pattern known as a flower pattern. Each flower pattern represents a sequence of profiles, one for each roll stand. These flower patterns are used to design and optimize the roll tools. The designers use computer simulation to develop and validate roll designs, as well as optimize the forming process.
The curving roll forming machine can form nearly any type of metal, from aluminum to stainless steel. Its versatility is unparalleled. It can handle almost any type of material, from nonferrous metals to pre-painted and polished metals. In fact, it can handle materials as thin as 0.005 inches. There are also options available for incorporating slots, holes, and slits. The curves can be as intricate as you like!
While roll forming is the most efficient method for manufacturing large quantities, the setup time can be considerable for a single part. Because of its high speed, these machines are ideal for producing massive amounts of finished material without much human interaction. Using a 200-foot-per-minute machine to produce 54 linear miles of material in a single minute would require a 12ft press brake to produce a finished part every 7.2 seconds.
The most important thing to consider in a curving roll forming machine is its ability to produce parts with curved profiles. It is capable of punching and cutting parts simultaneously, as well as rolling and forming them. The continuous roll forming process also facilitates the use of end straighteners. Compared to precut process, continuous roll forming process allows better control of parts and lowers the risk of end flare.
Curving roll forming is a common method of forming large metal plates and is also an effective method for producing aluminum coils. The process requires three rollers, and the angle between them determines the exact bend and angle. The basic form of roll forming is when the end product has a rectangular cross-section. Flat rolling is another method that uses two working rollers that rotate in opposite directions. The friction pushes through the material, which elongates it, but limits the amount of deformation that can be achieved in a single pass.
A curving roll forming machine may have several distinct features. Some of these features include the following: PLC control system, programmable logic controller, and laser welding. The PLC system controls the entire process, ensuring accuracy and minimal errors. Some of these features are available for additional kits. Some models are equipped with a laser or TIG welding unit to perform additional operations. Professional straightening machines ensure that the workpiece is formed in a single pass.
Tags:zinc roll forming machine | zinc sheet roll forming machine | zinc roof sheet roll forming machine
0users like this.
- Home
- New products
-
All Products
- Roof sheet roll forming machine
- Double/Three Layer Forming Machine
- Glazed Tile Roll Forming Machine
- C/Z/U Purlin Roll Forming Machine
- Floor Deck/Angle Jch Roll Forming Machine
- Light Steel Keel Roll Forming Machine
- Light Keel Villa House Roll Forming Machine
- Shutter Door and Door Frame Roll Forming Machine
- Roofing Ridge Cap Making Machine
- EPS Sandwich Panel Roll Forming Machine
- Cable Tray Roll Forming Machine
- Highway Guardrail roll forming machine
- Storage Shelves Roll Forming Machine
- Car Carriage Plate Roll Forming Machine
- 3d Wall Panel Roll Forming Machine
- Curving/Arch Roll Forming Machine
- Leveling shearing slitting machine
- Shearing & Bending machine
- Decoiler
- Industry Products
- Video
- Blog
- Contact
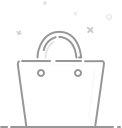
Your cart is currently empty.