News
Corrugated Plate Roll Forming Machine
Corrugated Plate Roll Forming Machine
A corrugated plate roll forming machine is used to produce a wide range of products made from metal sheets. These products are often used in shipping containers and the roofs of various buildings. Moreover, these products are durable and can resist damage from weather and weight loading.
The basic structure of a corrugated plate roll forming machine is a series of machining units that form the corrugated steel. The machining units include the de-coiler, the roll forming station, the cutting system, and the stacker. The entire forming process can be automated or semi-automated, and human operators are included in certain steps.
Decoiler
The first machining unit in a corrugated plate roll forming production line is the de-coiler. This machine is responsible for feeding the sheet metal coil into the forming stations and cutting systems. In mass production settings, such as the construction of corrugated steel roofing or corrugated steel for building shipping containers, this station is constantly working to feed the coils into the forming machines.
Once the coils have been fed into the forming stations, they will be compressed and pressed by the corrugated roll forming station. The forming machine has a set of worm-like rollers that press the metal sheet into a corrugated shape.
This bending technique is performed at room temperature and allows for precise, uniform shapes to be produced. Each set of worm-like rollers bends the metal slightly more than the previous one, which ensures that the desired cross-sectional configuration is maintained.
Each forming station also has an air pressure meter to gauge the amount of force being applied to the metal sheet as it passes through each station. This type of pressure measurement is vital in ensuring the quality of the finished product.
The forming station can have a hydraulic system or a pneumatic system to power the forming. Either system can be controlled by a computer. Once the forming system is in place, the corrugated steel sheet will be shaped and sent to the cutting system where it will be cut into a predetermined length.
Usually, the cutting system will be operated by a human operator or an automated machine. Depending on the specific needs of the company, the human operators or the automation machines can be placed in different locations within the forming station.
Another forming station is the cutting system, which uses either a hydraulic or a pneumatic system to cut the shaped corrugated steel into a final length. This system is also controlled by a computer and the end result of the cut can be gathered or processed at a terminal station.
Today’s modern roll forming machines feature CAD/CAM technology to maximize the efficiency of the bending process. This helps the forming machine function at its maximum potential, with programmable logic controllers tightening tolerance levels and minimizing errors. In addition, some of these modern machines include laser or TIG welding capabilities.
Tags:light steel keel villa roll forming machine | galvanized steel keel roll forming machine | shelf column roll forming machine | rack column roll forming machine
0users like this.
- Home
- New products
-
All Products
- Roof sheet roll forming machine
- Double/Three Layer Forming Machine
- Glazed Tile Roll Forming Machine
- C/Z/U Purlin Roll Forming Machine
- Floor Deck/Angle Jch Roll Forming Machine
- Light Steel Keel Roll Forming Machine
- Light Keel Villa House Roll Forming Machine
- Shutter Door and Door Frame Roll Forming Machine
- Roofing Ridge Cap Making Machine
- EPS Sandwich Panel Roll Forming Machine
- Cable Tray Roll Forming Machine
- Highway Guardrail roll forming machine
- Storage Shelves Roll Forming Machine
- Car Carriage Plate Roll Forming Machine
- 3d Wall Panel Roll Forming Machine
- Curving/Arch Roll Forming Machine
- Leveling shearing slitting machine
- Shearing & Bending machine
- Decoiler
- Industry Products
- Video
- Blog
- Contact
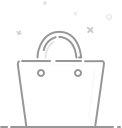
Your cart is currently empty.