News
Benefits of a Metal Sheet Profile Roll Forming Machine
Benefits of a Metal Sheet Profile Roll Forming Machine
A metal sheet profile roll forming machine bends or forms a strip of metal from coil to a desired cross-section.metal sheet profile roll forming machine The bending occurs between successive sets of rolls, changing the shape of the strip until it is formed into the desired cross-section (profile).
A variety of shapes can be made with this process: round, closed and C-shaped profiles are common, as well as a wide array of angles and box beams. These can be produced from aluminum and through 6 gauge steel (1/2'' thick) with varying degrees of precision.
The ability to form metals that are already painted, plated or coated is another benefit of this process. These can be shaped to a desired profile, and then the metal is welded, powder coated, or electroplated before they are cut to length. This is a time-saving feature that is not available with stamping or extrusion.
CNC controls the machine
Computerized roll forming machines use a programmable logic controller or PLC to control the operation of the system. The PLC decides when the system will perform a pre-feeding operation, the type of punching and notching needed to form the part, as well as other operations that are performed on the sheet metal. The PLC also programs the forming stations with the exact part geometries that are required to run a given profile.
Accuracy of the machine
If the roll forming process is a very critical step in your production, you will want a machine with very high accuracy and repeatability. This will help your company ensure that the parts you produce match the order specifications you have set for them, and you can also expect the metal to meet the quality standards of the customer.
Throughput of the machine
The rate at which a roll forming system produces parts depends on the material thickness, the number of roll stations and the amount of bending required to produce the product. A system can be capable of producing products at speeds up to 500 feet per minute.
Lubrication of the machine
A good lubrication of the roll forming machine helps to reduce tool wear, increase the speed of the process, and keep the components clean. This can be accomplished by a variety of lubricants including paraffin for non-ferrous metals, such as aluminum and copper.
Using the best equipment
The most effective roll forming machines have separate drive and forming rollers, which reduce the stress on the metal that they are working with. This can lead to increased durability and a longer life span for the components.
Choosing a quality machine
The best roll forming machine should be manufactured by a manufacturer that offers a long list of features and benefits, such as:
Separate drive and forming rollers allow for less stress on the metal in the forming process and help to make them last longer. They also help to reduce the force that the rollers need to apply to the material, which can make the forming process more efficient and can save you money over the lifetime of your machine.
Tags:horizontal roll forming machine | cable bridge roll forming machine | light steel keel villa roll forming machine
0users like this.
- Home
- New products
-
All Products
- Roof sheet roll forming machine
- Double/Three Layer Forming Machine
- Glazed Tile Roll Forming Machine
- C/Z/U Purlin Roll Forming Machine
- Floor Deck/Angle Jch Roll Forming Machine
- Light Steel Keel Roll Forming Machine
- Light Keel Villa House Roll Forming Machine
- Shutter Door and Door Frame Roll Forming Machine
- Roofing Ridge Cap Making Machine
- EPS Sandwich Panel Roll Forming Machine
- Cable Tray Roll Forming Machine
- Highway Guardrail roll forming machine
- Storage Shelves Roll Forming Machine
- Car Carriage Plate Roll Forming Machine
- 3d Wall Panel Roll Forming Machine
- Curving/Arch Roll Forming Machine
- Leveling shearing slitting machine
- Shearing & Bending machine
- Decoiler
- Industry Products
- Video
- Blog
- Contact
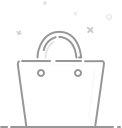
Your cart is currently empty.