News
Advantages of a Light Steel Keel Roll Forming Machine
Advantages of a Light Steel Keel Roll Forming Machine
A Light Steel Keel Roll Forming Machine is a metal-forming process that creates a shaped product from metal sheet or coil. The forming process is continuous and uses a group of rolls arranged in tandem to make incremental changes to the metal form until the designed profile section is reached. The process has a number of advantages over other methods of manufacturing similar shapes. These include lower energy costs, the ability to form hollow or semi-hollow structures and the ability to produce lengths that exceed what can be produced using other processes.
The resulting shapes are used in construction and a wide range of other applications. These include desk drawer slides, steel support framing, metal tubing and construction materials. Almost all metal related industries use roll forming because it offers benefits such as exacting tolerances, speed of production and dimensional accuracy.
There are three key engineering elements that determine the suitability of a material for roll forming: geometry, length and ductility. Often complex, multiple component parts can be reduced to a single shape using roll forming and this reduces the cost of design and assembly. The ability to bend the material to a desired radius also lowers material and labor costs.
Almost any metal can be formed through the roll forming process. This includes both ferrous and non-ferrous metals and their alloys. Metals that are malleable at a temperature below their melting point are suited for roll forming because they can be shaped without the need for additional heat treatment. The flexibility of the forming process is further enhanced by lubrication, which allows the rolling of the metal without damage to the surface or the tooling.
In addition to reducing the time required for production, the lubrication of the metal also reduces the energy required to move it through the forming process. This further decreases the cost of the manufacturing operation. Finally, the lubrication prevents damage to the completed product by reducing friction between the rollers and the metal.
A secondary operation that can be incorporated into the roll forming process is punching. This can be done in a variety of ways, including as part of the forming process or afterward as a separate operation. Punching can add features such as screw holes, chamfers, small side shear, pipeline hole and web foundation hole. It can even apply labels giving installation instructions as an in-line process. This enables the entire manufacturing process to be streamlined and consolidated into a single machine, which further reduces costs.
Tags:cable bridge roll forming machine | step ladder roll forming machine | light steel villa roll forming machine | shelf column roll forming machine
0users like this.
- Home
- New products
-
All Products
- Roof sheet roll forming machine
- Double/Three Layer Forming Machine
- Glazed Tile Roll Forming Machine
- C/Z/U Purlin Roll Forming Machine
- Floor Deck/Angle Jch Roll Forming Machine
- Light Steel Keel Roll Forming Machine
- Light Keel Villa House Roll Forming Machine
- Shutter Door and Door Frame Roll Forming Machine
- Roofing Ridge Cap Making Machine
- EPS Sandwich Panel Roll Forming Machine
- Cable Tray Roll Forming Machine
- Highway Guardrail roll forming machine
- Storage Shelves Roll Forming Machine
- Car Carriage Plate Roll Forming Machine
- 3d Wall Panel Roll Forming Machine
- Curving/Arch Roll Forming Machine
- Leveling shearing slitting machine
- Shearing & Bending machine
- Decoiler
- Industry Products
- Video
- Blog
- Contact
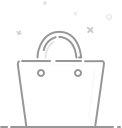
Your cart is currently empty.