News
Advantages and Disadvantages of an Aluminum Roll Forming Machine
Advantages and Disadvantages of an Aluminum Roll Forming Machine
Roll forming machines are designed to create metal components that have very complex cross-sections.aluminum roll forming machine Metals such as aluminum and steel are used, though some manufacturers have specialized equipment that can also use brass and copper. The process begins at room temperature with coils of metal that are guided into the first of many bending stations on the machine. Each station progressively bends the metal, creating the required shape. Depending on the design of the part, each station may have one or more roller dies. Lubrication is used to reduce friction between the rolls and the metal. Friction is an important part of the bending process and should not be eliminated, but rather controlled to prevent tool wear and other damage.
The resulting parts can be used in a variety of applications, including commercial building, manufacturing and aerospace industries.aluminum roll forming machine The process can produce a wide range of shapes, from simple straight profiles to very complex, contoured designs. Compared to other metal working processes, roll forming produces relatively low scrap amounts, typically only about 1% to 3% of the total production run.
Another advantage of the process is its ability to control the dimensional accuracy of formed parts.aluminum roll forming machine This feature is particularly important for high-volume orders, as it helps to keep labor costs down. Other forming methods such as casting and stamping are more suited to lower-volume orders, because they tend to be less accurate.
A key challenge when using a roll forming machine is maintaining proper tolerances, especially when the line is operating at high speed. Various factors can cause the metal to change shape and size, so careful attention must be paid to the entry shear to ensure that it is not misaligned with the machine. Similarly, the anti-flare fixtures on the machine must be properly configured to maintain consistent flare tolerances across all bends.
In addition, a number of factors can influence the quality of a finished part. One of the biggest challenges is controlling metal fatigue, which can occur in a number of ways, including deformation, shear, or compression. The physics of metal fatigue is complex, but one way to minimize it is by using hard-drawn steel. Another strategy is to use softer, higher-melting metals, such as aluminum or brass, which will not oxidize.
Although the shape of a finished part is limited by the capabilities of the forming process, the advantages of the technology make it an excellent choice for producing large volumes of parts with complex shapes. This is a critical consideration for automotive structural components, which often require long, thin longitudinal members. While these parts could be produced by other methods, such as extrusion, the cost of the material and the limited lengths available would make them uneconomical. For these applications, the roll forming method is ideal. By using a hardened alloy such as aluminum, these parts can be made at a reasonable price and still meet the required strength and stiffness standards. This makes them a good choice for use in modern vehicles.
Tags:shelf rock roll forming machine | car panel roll forming machine | zinc sheet roll forming machine
0users like this.
- Home
- New products
-
All Products
- Roof sheet roll forming machine
- Double/Three Layer Forming Machine
- Glazed Tile Roll Forming Machine
- C/Z/U Purlin Roll Forming Machine
- Floor Deck/Angle Jch Roll Forming Machine
- Light Steel Keel Roll Forming Machine
- Light Keel Villa House Roll Forming Machine
- Shutter Door and Door Frame Roll Forming Machine
- Roofing Ridge Cap Making Machine
- EPS Sandwich Panel Roll Forming Machine
- Cable Tray Roll Forming Machine
- Highway Guardrail roll forming machine
- Storage Shelves Roll Forming Machine
- Car Carriage Plate Roll Forming Machine
- 3d Wall Panel Roll Forming Machine
- Curving/Arch Roll Forming Machine
- Leveling shearing slitting machine
- Shearing & Bending machine
- Decoiler
- Industry Products
- Video
- Blog
- Contact
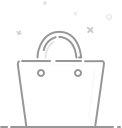
Your cart is currently empty.