News
Factors to Consider When Choosing a Corrugated Plate Roll Forming Machine
Factors to Consider When Choosing a Corrugated Plate Roll Forming Machine
When choosing the right corrugated plate roll forming machine for your fabrication operation there are many factors to consider including the type of materials you work with and the types of shapes that you need to make.corrugated plate roll forming machine In addition to considering the dimensions of the roll you need to choose a machine that can handle the capacity for the amount of production you need. Plate rolling machines are capable of both static and dynamic bending which is where the sheet metal is held stationary as a roll bends it upward, as opposed to a press brake where the material is forced into the desired shape.
Dynamic bending is more efficient because the operator doesn't have to physically push the material into position for each forming pass. This makes it easier to get consistent results and reduces the time required for each part. However, static bending is also an effective method of producing quality parts if done correctly and can be used to create complex or intricate forms.
The type of bending process you use will also influence the machine you choose. If you will be working with heavy-duty plates that are a high-strength and thick, then it's important to look for a heavier model. The machine will have to be equipped with heavier, more durable forming rolls to ensure that it can take the load and provide the strength necessary for your projects.
If you're planning to work with lighter materials, then it may be a better fit for you to select a light-capacity model. These are electromechanical or hydraulic and typically work by pinching the flat sheet between two vertically opposed rolls to pre-bend both ends. Some have side rolls that can move close under the top to allow for a wider variety of bending and can be tilted for cone bending.
Another factor that influences the size of the plate roll you need is the maximum width that it can bend in a single pass. A higher-capacity machine has the ability to bend a larger strip of material in a single pass. However, the roll's physical length will also affect this capacity as the longer it is the more force that it has to apply and the more stress that it generates when bending thinner strips of material.
A last factor to consider is the thickness of the material you want to roll. This will determine the number of forming and pressing rolls you need and will impact the diameter of the rolled piece. It's also important to consider the yield and tensile strength of the material as this will help you determine the minimum and maximum diameters that your project requires.
It's essential to select the correct size of plate roll for your applications because if you purchase a machine that's too small, it will be difficult or impossible to produce the desired results. You should also pay attention to the quality of the machine and how sturdy it is, as well as its features such as a digital readout or CNC control system.
0users like this.
- Home
- New products
-
All Products
- Roof sheet roll forming machine
- Double/Three Layer Forming Machine
- Glazed Tile Roll Forming Machine
- C/Z/U Purlin Roll Forming Machine
- Floor Deck/Angle Jch Roll Forming Machine
- Light Steel Keel Roll Forming Machine
- Light Keel Villa House Roll Forming Machine
- Shutter Door and Door Frame Roll Forming Machine
- Roofing Ridge Cap Making Machine
- EPS Sandwich Panel Roll Forming Machine
- Cable Tray Roll Forming Machine
- Highway Guardrail roll forming machine
- Storage Shelves Roll Forming Machine
- Car Carriage Plate Roll Forming Machine
- 3d Wall Panel Roll Forming Machine
- Curving/Arch Roll Forming Machine
- Leveling shearing slitting machine
- Shearing & Bending machine
- Decoiler
- Industry Products
- Video
- Blog
- Contact
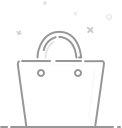
Your cart is currently empty.