News
Double Layer Roll Forming Machine
Double Layer Roll Forming Machine
Double layer roll forming machines allow manufacturers to produce two different profiles simultaneously, allowing them to increase efficiency and productivity. They are a great choice for industries that require precision, quality, and customization.
Double-layer profile roofing sheets are ideal for commercial buildings, apartments and villas, as well as green buildings seeking sustainability certification. The extra layer of insulation provides enhanced thermal and acoustic performance and improves building durability. They can also reduce noise levels and provide fire protection. The process is customizable and suitable for various roofing materials.
Roll forming machines use long coils of metal that are automatically fed into the machine, reducing labor costs. The resulting products have tight tolerances and clean contours, eliminating the need for deburring or trimming of flash. The process requires minimal heat and does not damage metals, minimizing energy costs. The machines can be customized to shape complex cross sections and intricate patterns, expanding the range of construction possibilities. The design of the machines makes them easy to maintain and repair.
In addition to ensuring safety, regular inspections and maintenance of the machines can prevent downtime and costly repairs. Keeping an inventory of essential spare parts ensures that the company is prepared for unforeseen breakdowns. Regularly check the electrical components, wiring and safety systems of the equipment to ensure that everything is functioning properly. Regularly test emergency stop buttons, sensors and interlocks to ensure that they work properly.
Performing routine maintenance and inspections on the double layer roll forming machine helps to prevent major problems and keeps the production line running smoothly. This is especially important when the machine is producing high volumes of product, as downtime can have a direct impact on the bottom line. Identifying the most common issues and addressing them quickly helps to minimize downtime and maximize productivity.
The design of double layer roll forming machines allows them to operate for extended periods with little or no downtime. The machines are designed with high-quality materials and are built to withstand heavy-duty operation. With regular inspections and maintenance, these machines can run reliably for years without requiring significant repairs or replacement parts. The reliability of these machines makes them a cost-effective option for businesses that need to meet high volume demands.
To achieve this high level of reliability, the machines are constructed with careful attention to details. They are lubricated to reduce friction between the rolls and the metal, preventing wear. The lubrication also reduces the temperature of the metal to prevent damage during the bending process. Regular lubrication of moving parts also reduces energy costs, since the machine does not need to be heated as it performs its function. The lubrication prevents the formation of oxide layers, which could otherwise cause corrosion and other problems. By avoiding unnecessary heating and lowering energy costs, the double layer machine offers significant savings over traditional machinery.
Tags:ceiling stud roll forming machine | container sheet roll forming machine | ibr roof sheet roll forming machine
0users like this.
- Home
- New products
-
All Products
- Roof sheet roll forming machine
- Double/Three Layer Forming Machine
- Glazed Tile Roll Forming Machine
- C/Z/U Purlin Roll Forming Machine
- Floor Deck/Angle Jch Roll Forming Machine
- Light Steel Keel Roll Forming Machine
- Light Keel Villa House Roll Forming Machine
- Shutter Door and Door Frame Roll Forming Machine
- Roofing Ridge Cap Making Machine
- EPS Sandwich Panel Roll Forming Machine
- Cable Tray Roll Forming Machine
- Highway Guardrail roll forming machine
- Storage Shelves Roll Forming Machine
- Car Carriage Plate Roll Forming Machine
- 3d Wall Panel Roll Forming Machine
- Curving/Arch Roll Forming Machine
- Leveling shearing slitting machine
- Shearing & Bending machine
- Decoiler
- Industry Products
- Video
- Blog
- Contact
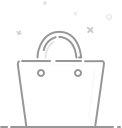
Your cart is currently empty.